The Importance of Third-Party Inspections on Workplace Machinery in South Africa
- Duan Coetzee
- Sep 27, 2024
- 3 min read
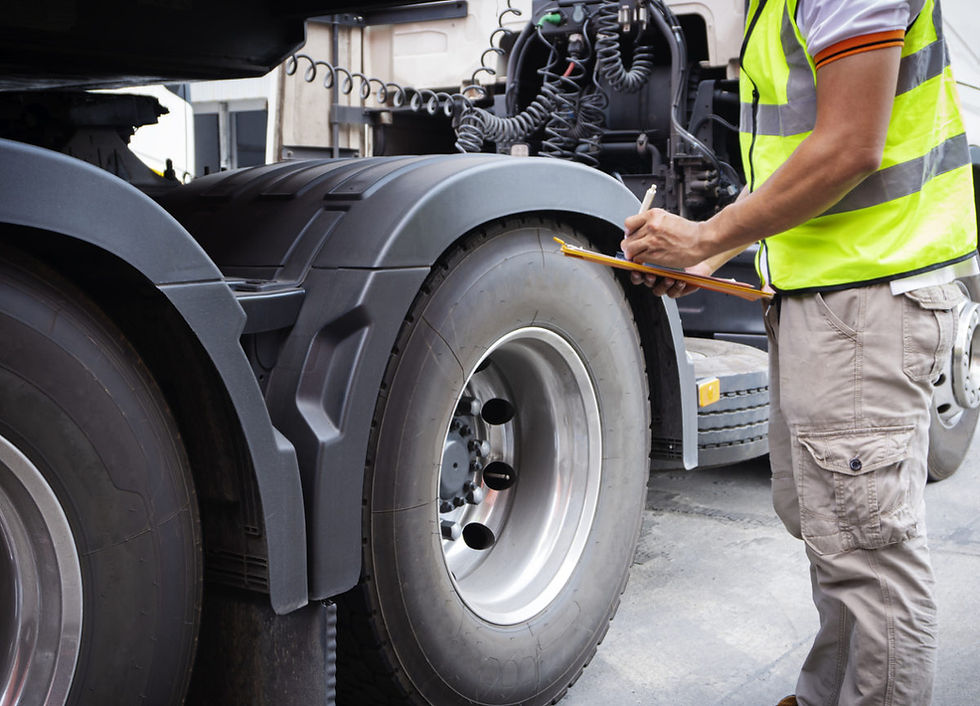
In South Africa, the industrial landscape is diverse, encompassing mining, manufacturing, construction, and agriculture. Each sector relies heavily on machinery to maintain efficiency and productivity. However, with this dependence comes the responsibility of ensuring that all equipment operates safely and effectively. This is where third-party inspections play a vital role. These independent assessments not only enhance safety but also contribute to operational efficiency and compliance with legal regulations.
Enhancing Safety Standards
One of the primary reasons for conducting third-party inspections is the enhancement of safety standards. Independent inspectors bring expertise and objectivity, ensuring that machinery is evaluated without bias. This external perspective is crucial in identifying potential hazards that internal teams might overlook. By rigorously assessing equipment, third-party inspections help prevent accidents and injuries, protecting workers and promoting a safer workplace.
Ensuring Compliance with Regulations
South Africa has stringent regulations governing workplace safety and equipment standards, particularly under the Occupational Health and Safety Act (OHSA) and the Mines Health and Safety Act (MHSA). Non-compliance can result in severe penalties, including fines and shutdowns. Third-party inspections ensure that machinery meets all legal requirements, helping organizations stay compliant. By providing documented evidence of adherence to safety standards, these inspections safeguard businesses against legal repercussions and enhance their credibility in the marketplace.
Improving Operational Efficiency
Regular inspections by third-party experts can lead to improved operational efficiency. During the assessment process, inspectors often identify inefficiencies, such as equipment that is not operating at optimal levels or maintenance practices that are inadequate. Addressing these issues can lead to reduced downtime and lower maintenance costs. When machinery operates efficiently, productivity increases, ultimately benefiting the bottom line.
Extending Equipment Lifespan
Machinery is a significant investment for any organization. Regular third-party inspections can help extend the lifespan of this equipment by identifying wear and tear before it becomes a critical issue. Early detection of potential problems allows businesses to conduct timely repairs, avoiding costly breakdowns and replacements. This proactive approach not only saves money but also ensures that operations run smoothly without unexpected interruptions.
Building Trust with Stakeholders
Third-party inspections foster trust among various stakeholders, including employees, clients, and regulatory bodies. By demonstrating a commitment to safety and compliance through independent assessments, businesses can enhance their reputation. This transparency builds confidence among employees, knowing they work in a safe environment, and assures clients that the company prioritizes quality and safety. A strong reputation can lead to increased business opportunities and partnerships.
Promoting a Culture of Safety
Incorporating third-party inspections into the operational routine promotes a culture of safety within organizations. When employees see that safety is prioritized through regular, independent evaluations, they are more likely to adopt safe practices themselves. This cultural shift can lead to increased vigilance regarding safety protocols and a collective commitment to maintaining a safe working environment.
Conclusion
In conclusion, third-party inspections of workplace machinery in South Africa are essential for ensuring safety, compliance, and operational efficiency. By providing objective assessments, these inspections enhance safety standards, protect businesses from legal ramifications, and promote a culture of safety among employees. Additionally, they contribute to the longevity of machinery and overall productivity. As South Africa continues to develop its industrial landscape, the importance of third-party inspections cannot be overstated. Investing in these assessments is not just a regulatory requirement; it is a critical component of responsible and sustainable business practices that ultimately lead to a safer and more productive workplace.
Hitting the nail right on the head in enhancing safety in our Mines and Works.